Projekte
SMED – Rüstworkshop an zwei großen Pressen
Problem:
Rüstzeit über 120 Min.
Ansatz:
- 5-Tage-SMED-Workshop, 8 Teilnehmer, Vollzeit (1 SV, 2 TL, 2 AF, 1 AN, 1 WZG-Macher, 1 Berater)
- Filmaufnahmen
- Zerlegung und Gliederung in externe und interne Einzel-Vorgänge.
- Variables Rüstteam nominiert (1 TL 1 AF 1 AN 1 WZG-M.).
- Rüstvorgänge werden früh angekündigt und durch TL vorbereitet.
- Trainings für TL, AF und AN z.B. für Kranbedienung.
- „Areas of Activities” pro Rüst-Mitarbeiter definiert.
- Schnellspanner, „Plug-and-Connect“-Verbinder, Anschläge, … .
Legende: SV: Supervisor / Meister; TL: Teamleiter; AF: Anlagenführer; AN: Abnehmer; WZG-M.: Werkzeugmacher.
Resultat: Rüstvorgang konnte um 30% auf 75 min. gesenkt werden. Aussicht auf weitere 20% nach zwei Wochen.
Anmerkung:
Aufgrund der Infrastruktur (Rüsten mit Stapler, Deckenkran, beengter Platz, umständliche Stanzabfallentsorgung, ect. liegt diese Rüstzeit noch weit entfernt von den heute üblichen Rüstzeiten von großen Pressen.
Hydraulik-Öl, Standzeit durch Nebenstromfilter verlängern
Situation: In diesem Werk wurden mit 8 hydraulischen Pressen bis 4.000 kN Presskraft Sitzschienen für Kfz gefertigt.
Problem: Das Hydrauliköl verschmutze durch Abrieb relativ schnell und musste jährlich ausgetauscht werden.
Lösung: Anschaffen von zunächst einem Nebenstromfilter. Dieser filterte das Öl während der Produktion auf eine Partikelgröße von weniger als 10 Mikrometer. Qualitätsmessungen an dem Öl wurden regelmäßig aller drei Monate durchgeführt.
Resultat: Die Standzeit verdoppelte sich fast und es konnte so pro Presse mit 2.500 l HLP46-Hydrauliköl Kosten von 9.000 Euro pro Jahr vermieden werden.
Lieferengpass / SCRUM
Situation: Tier 1. Presseninsel (U-Form, Schwenkarm-Transfer) mit Presskräften von 1.500 bis 2.000 kN. Automatische Zuführung von Platinen, Produkte automatisch als Schüttgut in Gitterbox. Ein Anlagenführer.
Problem: Werkzeugbrüche und häufige Störungen. Geringe O.E.E.. von etwa 40%. Sonderfahrten.
Ansatz:
- Untersuchung der Ursachen u.a. mit Zeitraffer-Film (Werkzeug- und Transfer-Schwingungen sichtbar)
- Festes Team zur Lösung dieses spezifischen Prodblems gebildet: 2 AF, 2 TL, 1 WZG-M., 1 Inst.-Halter, 1 Interim Manager als KVP-Koordinator.
- Planung, Problemanalyse, Tracking und Aufgaben-Erledigung fand während der Arbeitszeit statt und wurde über eine SCRUM-Methodik gesteuert.
- Standardisierung von Einstell-Vorgängen: "An welcher Presse / an welchem WZG wird wie parametrisiert?"
- Einführung von 55 / TPM
- Einbeziehung von Management in einem "weekly Reporting" durch das Shopfloor-Team.
Lösung:
- Es stellte sich heraus (Zeitraffer-Kamera), dass ein WZG-Oberteil sich von selbst löste, weil die Spannfixierung zu schwach ausgelegt war. --> Wechsel auf stärkere Spanner
- Die beiden AF verwendeten unterschiedliche Methoden zur Parametrisierung. --> Standardisierung und Training
- Viele kleine Mängel wurden während des Workshops bemerkt und behoben.
- Die Schmierstoffbehälter von nur 1 Liter Vorrat wurden gegen größere ausgetauscht, sodass bei 7 Pressen nicht jede Schicht ein System-Stopp eintrat, welcher ein Eingreifen erforderte. Die Behälter wurden einmal pro Woche befüllt.
Resultat:
- Die Sonderfahrten konnten nach 4 Wochen abbestellt werden. Von 19 Schichten wurde auf 15 Schichten umgestellt, bei leicht gesteigerter Ausbringung.
- Die größte Erkenntnis lag jedoch am Team-Spirit und an dem zunehmenden Selbstbewußtsein der Mitarbeiter vom Shopfloor, wenn freitags der Werkleiter nach dem Fortschritt fragte und ihm Erfolge präsentiert werden konnten.
ANDON / MES im Presswerk
Problem: Hoher Produktivitätsverlust an den Pressen durch fehlende Aufmerksamkei
Ansätze: (Durch Auftraggeber bereits umgesetzt):
- Andon-Terminals wurden aufgestellt, etwa 1 Terminal für zwei Pressen.
- AF / TL melden Aufträge erfüllt und bestellen Coils, Werkzeuge und Leergut.
- Beauftragen Intralogistik für den Abtransport von Vollgut.
- Melden Störungen und fordern Unterstützung an.
- Zentrale Verwaltung der Daten in einem MES-System.
- ANDON-Displays an der Hallendecke.
- Status-Übersicht von jeder Presse auf Mobil Devices.
- Mehr als 10 Statusmeldungen, von Werkzeug-Störung, über Rüsten, bis hin zu Personalmangel
- Anzeige von Ist-/Soll-Hubzahl, erreichte Stückzahl gegen Auftragsvolumen
- Plan: Pro Presse ein ANDON-Stack light zur Anzeige von 5 Basis-Status.

Ausschnitt aus einem ANDON-Board. Anzeige der Stillstände und der erreichten Hub-Zahlen.
5S / TPM im Presswerk
Problem: Produktivitätsverluste lassen sich auf ein Anlagenversagen zurückführen
Situation: Die Anlagen (Pressen, Vorschub, Richteinheit, Beölung, Schütten zur Entsorgung von Stanzabfall, Förderbänder) sind extrem verschmutzt und lassen eine vorbeugende Inspektion ihres Zustandes nicht zu.
Ansätze:
- 5S und TPM gehen Hand in Hand und werden als ein "Tool" eingeführt
- Grundlreinigung der gesamte Anlage an Wochenenden, Inspektion und Reparatur durch Fachpersonal.
- Mitarbeiter wurden vor Ort an Ihrer Anlage von der Instandhaltung geschult.
- Das Personal der Anlage (TL, AF, AN) erhalten maßgeschneiderte Inspektionsaufgaben.
- Produktionsfreie Zeiten und das Schichtende werden genutzt, um einfache Wartungen durchzuführen.
Resultat:
Die Micro-Stopps, also die Kurzunterbrechungen, nahmen sofort merklich ab, was sich auf die Leistung der Anlage und auf den O.E.E. positiv auswirkte.

Eine der Pressen während der Einführung von 5S / TPM. Trotz des hohen Alters kann eine gut gepflegte Presse eine hohe Verfügbarkeit und Produktivität erreichen.
Umformschmierstoff einsparen
Situation: In diesem Werk wurden mit ca. 40 Pressen unterschiedlicher Presskraft eingesetzt, welche fast ausschließlich mit Metallband vom Coil versorgt wurden.
Wir haben uns als Modellanlage eine Folgeverbund-Presse mit 4-m-Tisch und Sprühbeölung ausgesucht.
Problem: Allgemein wurde zu viel Öl aufgetragen. Dieses floss in die unteren Werkzeughälften und von dort in den Pressentisch und in den Pressenkeller. Auch wurden die Wege in der Halle beim Abtransport der Werkzeuge (Stapler) gefährlich verschmutzt. Ein Anliegen war auch, durch geringere Ölmengen Kosten zu vermeiden.
Ansatz: Für drei A-Produkte wurden die Parameter (Pressen-Hub pro Minute, Vorschub in mm, Sprühzeit in s und Öl-Förderdruck in Pa) eingestellt und die entsprechende Öl-Marke eingefüllt. Es gab drei Öl-Viskositäten, eine davon legiert mit MoS2)
Die Presse lief im Leerlauf ohne Werkzeug.
Die Sprüh-Menge von zwei Düsen wurde in einer Plastikwanne aufgefangen, während 100 Pressen-Hüben.
Die Menge wurde gewogen und auf die Fläche umgerechnet, die sich aus dem Abstand der Düsen zueinander und dem Vorschub ergab.
Die Ölmengen wurde mit über 50 g/m2 bestimmt und als deutlich zu hoch bewertet. Bei den schweren Umformungen von Blech mit einer Festigkeit von 650 N/mm2, 3 mm Dicke und „scharfen“ Radien (siehe Foto) wurde ein Zielwert von 25 g/m2 angestrebt. Alle anderen Umformungen bekamen zunächst einen Zielwert von 10 g/m2. Besonders leichte Umformungen, etwa das Prägen von Alu-Blech bekam den Zielwert von 5g/m2.
Lösung: Die Sprühparameter wurden entsprechend verstellt und mittels Wiegen überprüft. Dann mussten sich diese neuen Einstellungen in der Praxis bewähren. Dazu waren eine Q-Labormitarbeiterin und ein Werkzeugmacher zugegen.
Resultat: Die reduzierten Mengen waren immer noch ausreichend, um Werkzeuge zu schonen und eine gute Produktqualität zu gewährleisten. Eine über alle drei Ölsorten angenommene mögliche Reduzierung um 50% über alle Pressen und Produkte ergab eine jährliche Einsparmenge von über 11.000 EURO und eine nicht näher bezifferte Einsparung von Reinigungsmittel in den anschließenden Teilereinigungsanlagen.

GAP Analyse von 5 Fabriken
Situation: Ein Zulieferer (Tier 1) zur Herstellung von Kabelbäumen meldet gestiegene Preise für Rohstoffe, Personal und Logistik an. Er fordert von seinem Kunden OEM bereits für das laufende Jahr eine Nachzahlung in Höhe von 14 Mio. EURO.
OEM beauftragt eine Beratungsfirma, die Kosten den Tier 1 zu analysieren und eine Entscheidungsgrundlage zu schaffen, aufgrund der sich der OEM entschließen kann, sich an den Kosten zu beteiligen.
Ansätze: 5 Werke wurden analysiert (je eine Woche). EinTeam von 4 Experten (Produktionsorganisation, SCM, Purchasing und Finance) analysierten im Detail die jeweiligen Bereiche.
Resultat: Insbesondere in der Produktion konnte erhebliche Verschwendung identifiziert werden und Maßnahmen zur Optimierung aufgezeigt werden. Personal-Auslastung war gering, NRFT-Quote war hoch, Anlagenausfälle häufig und Rohstoff-Schwund aus ungesicherten Lägern wurden identifiziert. Eine unvorstellbar umständliche Logistikkette mit zum Teil 50 Tage Transit-Zeit trugen dazu bei, dass Technische Änderungen nicht rechtzeitig einfließen konnten und Produkte abgeschrieben werden mussten.
Im Gegensatz dazu konnte von meine Kollegen attestiert werden, dass Preise für Rohstoffe und Personalbeschaffung deutlich gestiegen sind.
Der OEM entschied sich dazu, etwa die Hälfte der angemeldeten Kosten zu tragen.

Weitere Arbeitsschwerpunkte
- Fabrikplanung: Auslegung von Pressen, Biegeinseln und Hydroformanlagen.
- Beschaffung einer 5-stufigen, mechanischen Transferpresse (12.500 kN).
- Managementsysteme IATF 16949, ISO 50001 und ISO14001 eingeführt.
- Prozess-Benchmark für Standardprozesse in der Blechverarbeitung.
- Facility-Management definiert und extern vergeben.
- Entwicklung von Walzen- und Sprühbeölungssystemen für Pressen.
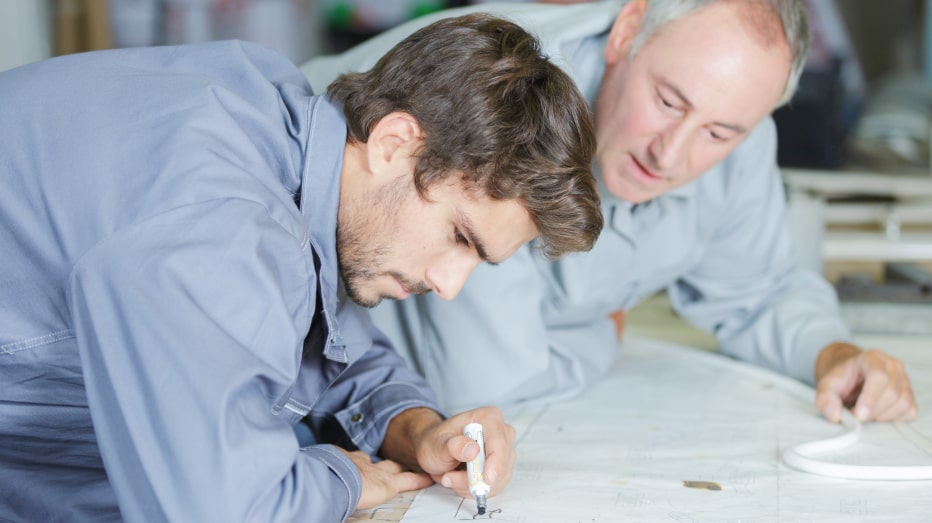